So this is the one that I pulled out all of the stops. I learned in my other knives that I didn’t have the experience to make proper hand-sanded bevels that were uniform, so I made a bigger table for my sander and then I made a simple bevel jig. I started sanding and brought out some of the texture in the steel and realized it was still too thick and the bevels were terrible so I thinned the blade and using my new jig made a nice saber grind bevel.
Then the sanding started. I ground to 400 grit on my belt sander and then dropped down to 320 by hand and worked my way all the way up to 2000 grit. Then I got to play with the chemicals. I made a Ferric Chloride solution using roughly 150ml of Ferric Chloride to about 1250ml of Distilled water. I also made about 1500ml of instant coffee using half of the container of coffee. This is pulled directly from watching Neil Kamimura, the bladesmith from Hawaii.
While etching the blade in roughly 5 minutes increments, between etches I sanded from 1500 grit all the way to 3000 grit. between sanding and etches I rinsed the blade with distilled water as to not contaminate my Ferric Chloride solution. After the final sand and rinse I dropped it into the strong coffee solution for about an hour and 20 minutes, the coffee brought a real nice dark color to the 1085 while still leaving the 15n20 nice and bright. I hit the knife with compressed air to dry it off and then put a nice coat of wax on there to lock in the color. I couldn’t find my heat gun to really lock it in but it was 90 degrees in the shop so I figured it would be okay.
I was going to go very intricate with the handle but I decided against it last minute because I wanted to highlight the pattern in the blade so I want with a simple Wa-Style Handle using ebony and olive wood. I didn’t know that sanding olive would on the belt sander would make the workshop smell like a dirty martini but it did. I was not a fan.
I took it to work, and the chefs loved it, and better yet it performed beautifully and I loved it.
8-inch Kiritsuke Kinfe - 173g
2.0mm spine thickness flat ground at 1.3 degrees with a micro-bevel to strengthen the edge.
Steel is 256 layer Damascus of 1095 and 15N20 with a hardness of 59HRC +/-1
The next step is I’m waiting on my 2x72 belt grinder so I’ll have real knife-making tools, and I’m excited to see what I can do with that. I’ve ordered more materials to make some more knives and stuff to make the workshop flow better I’m so very excited to see what the next project is.

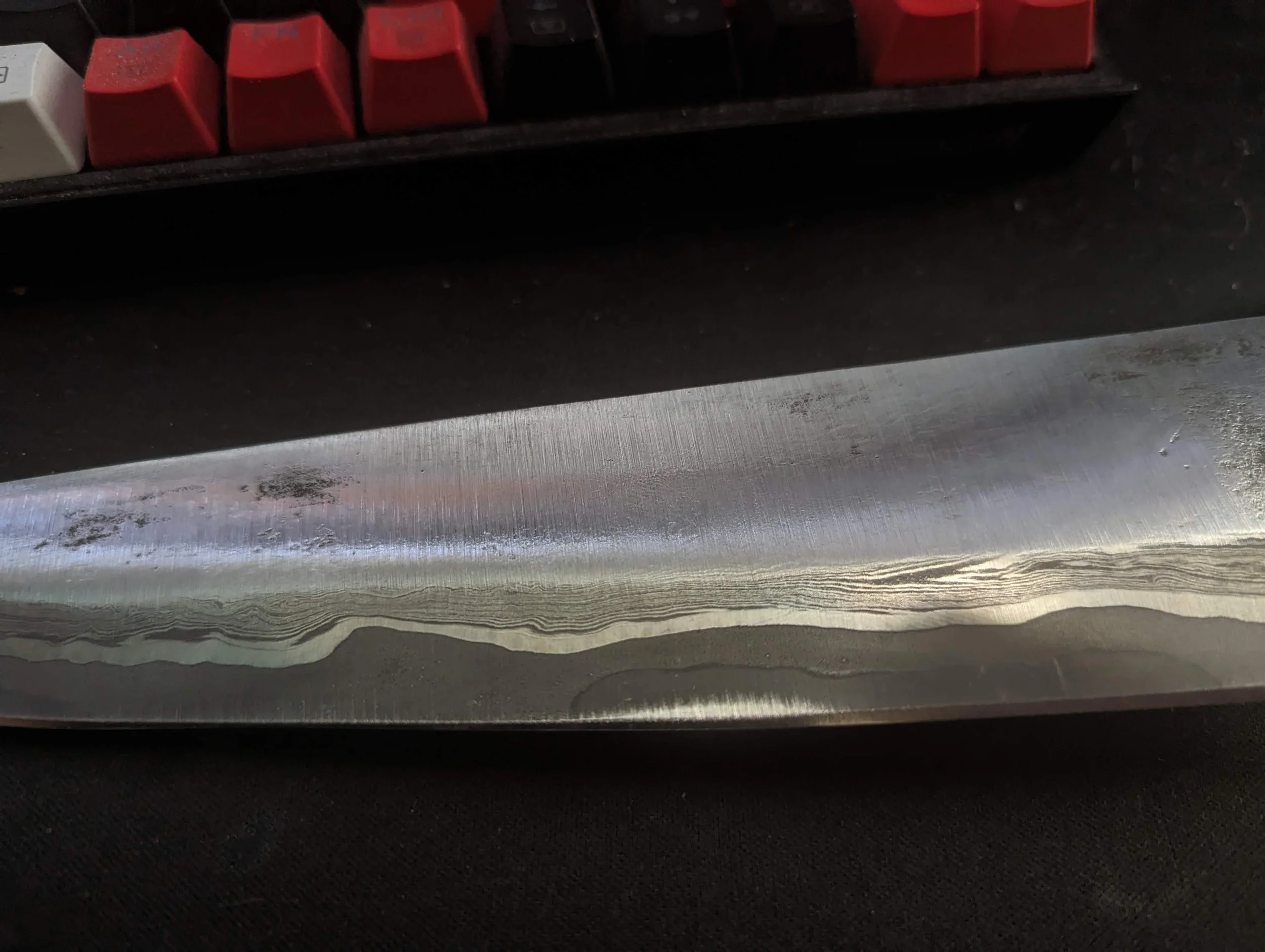
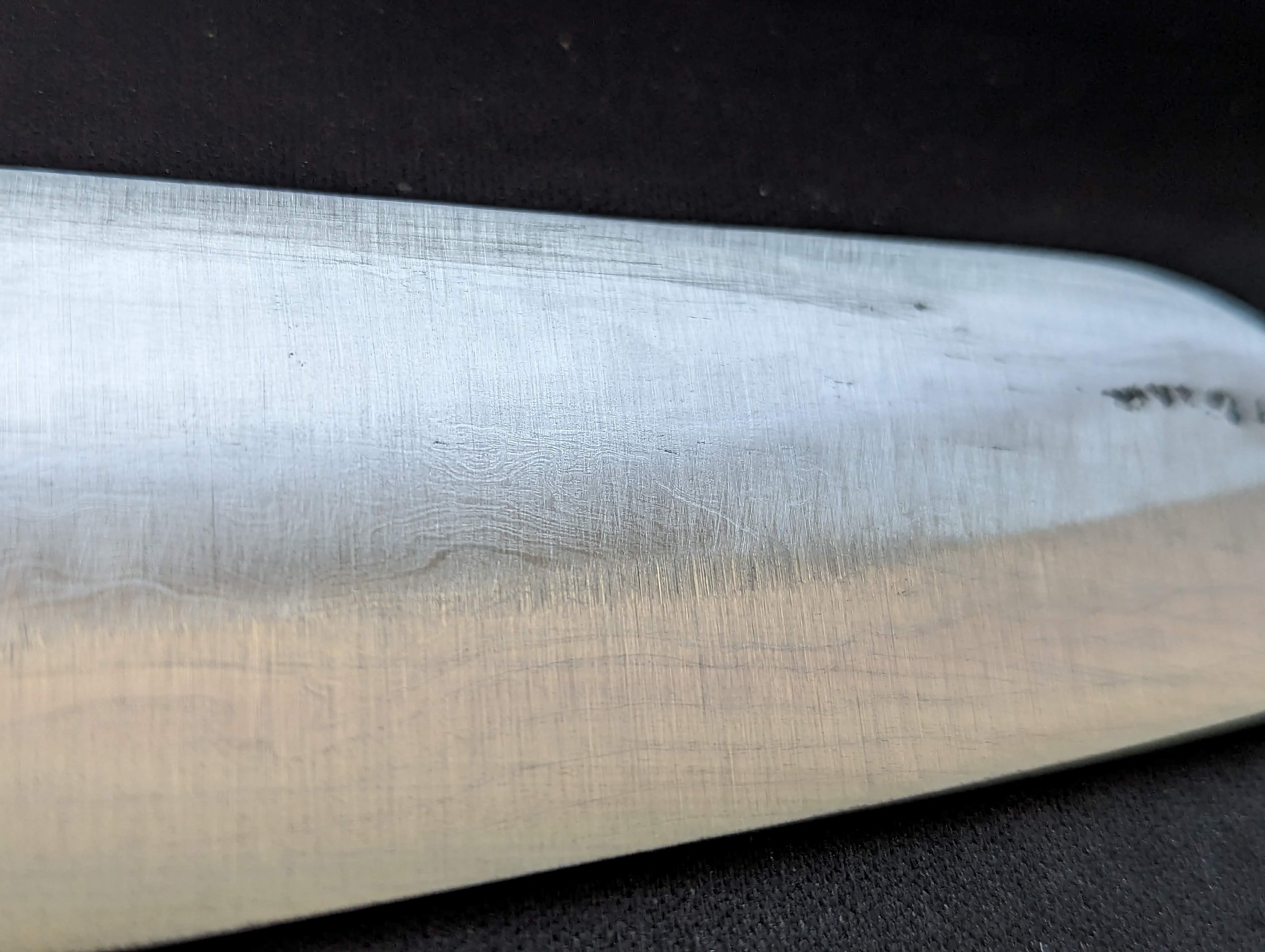
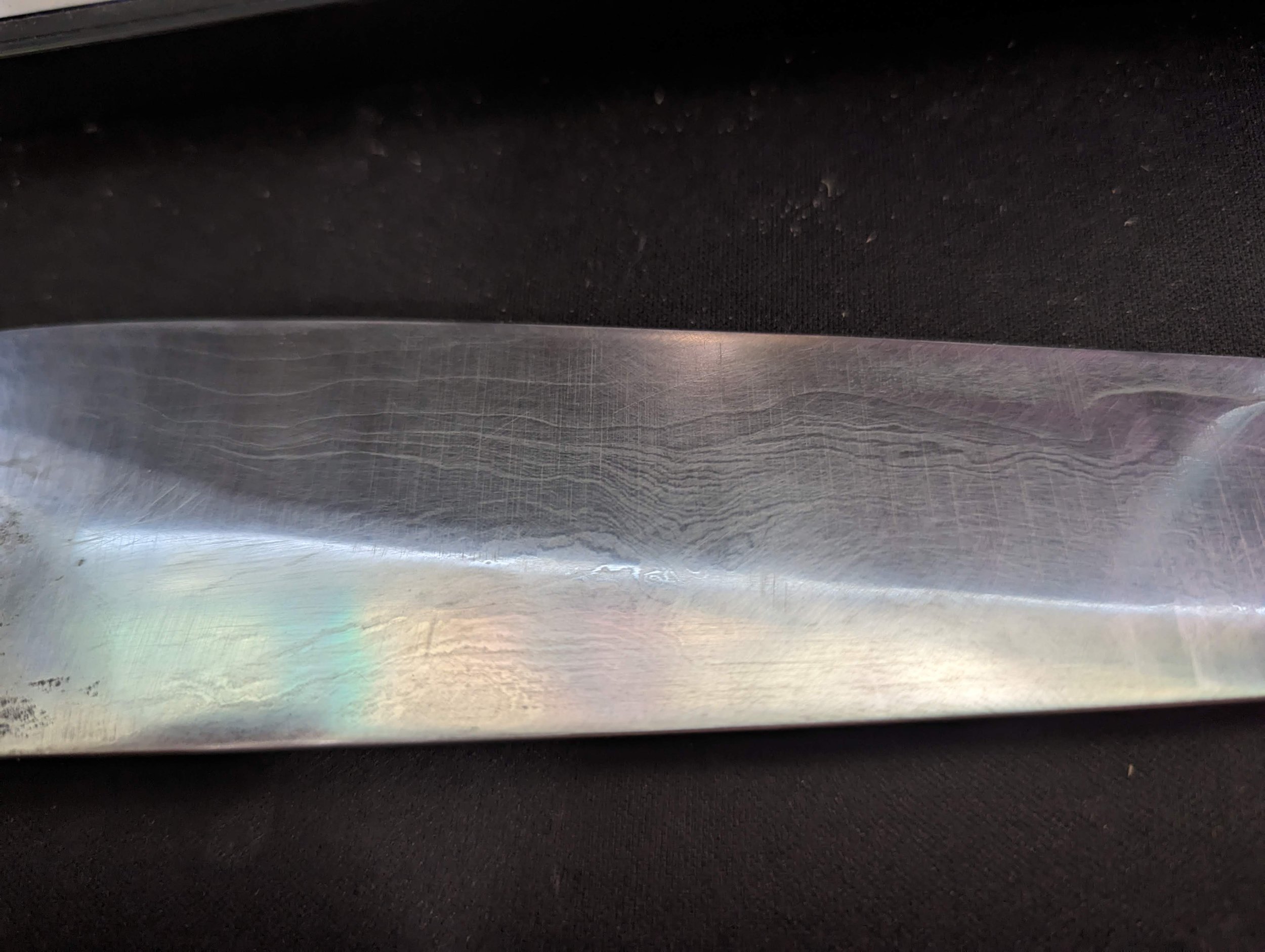
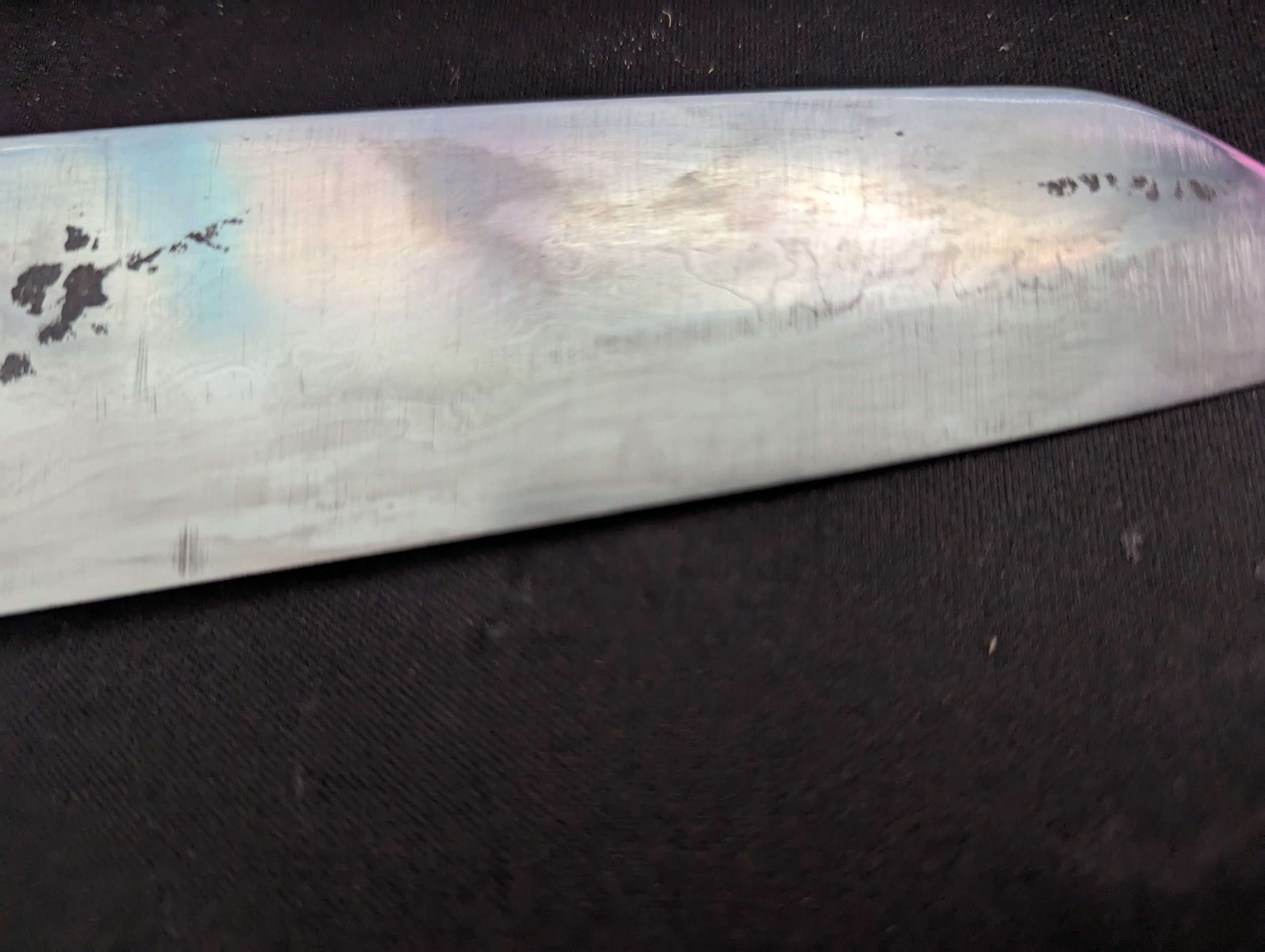



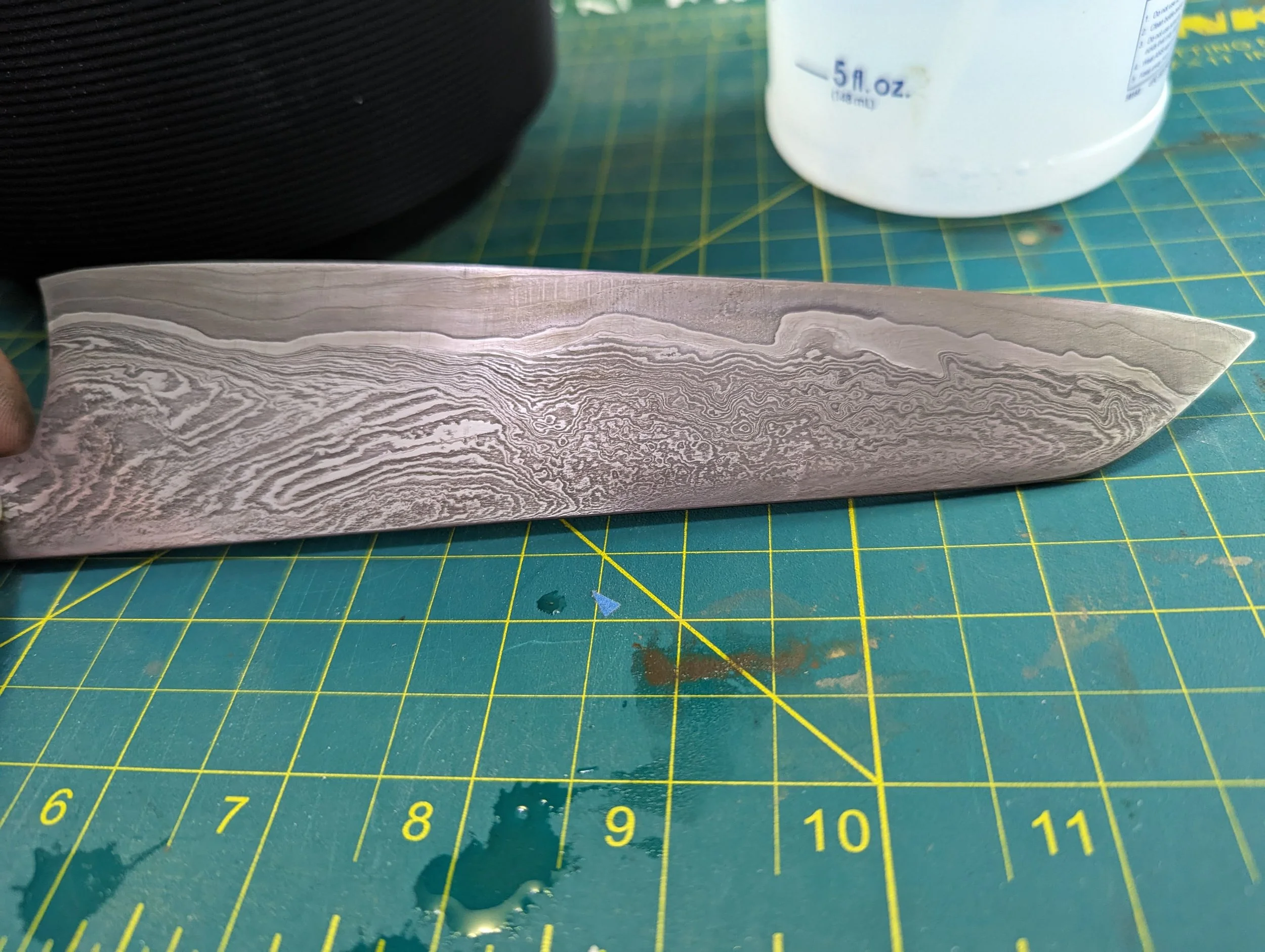
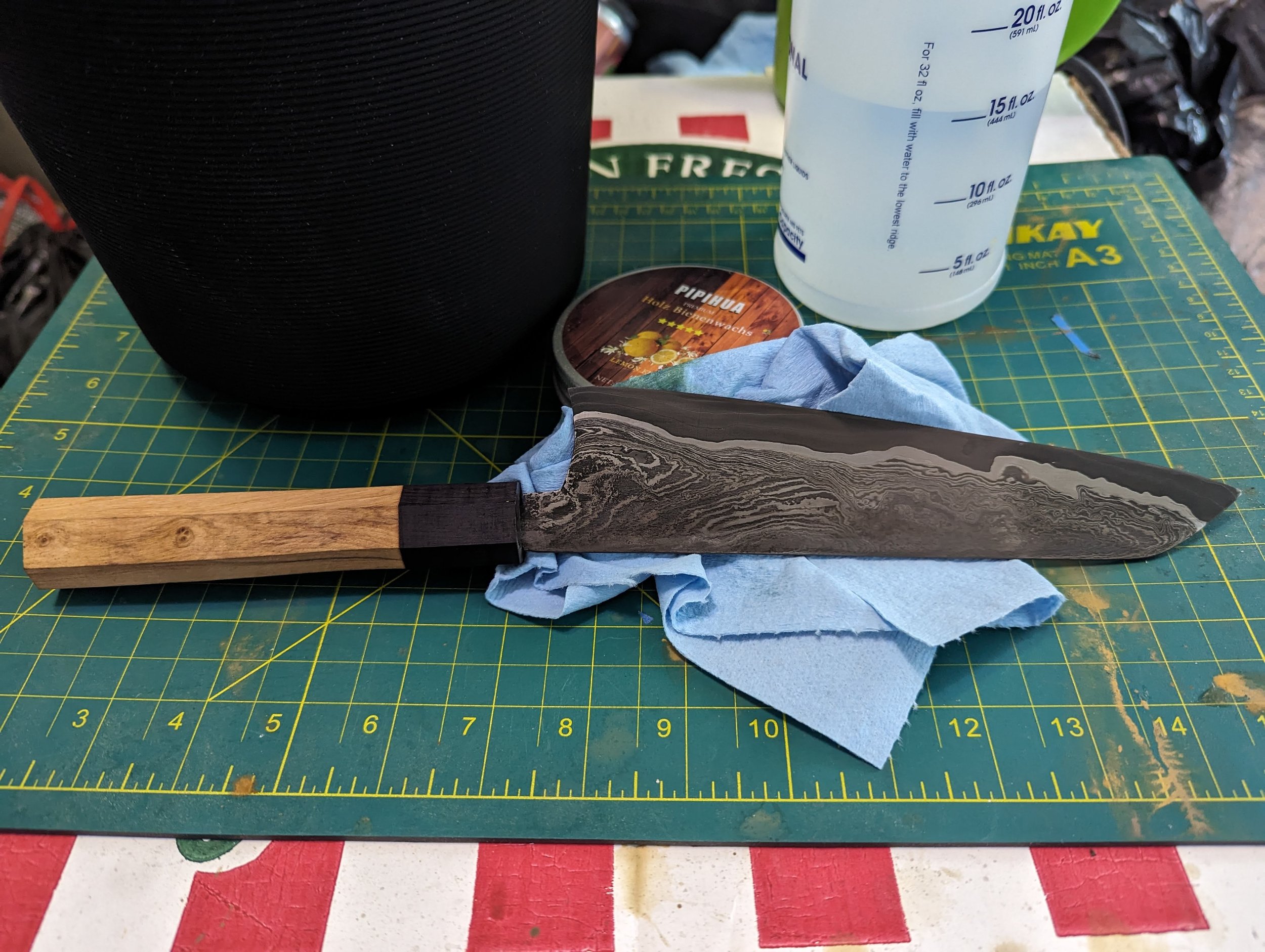

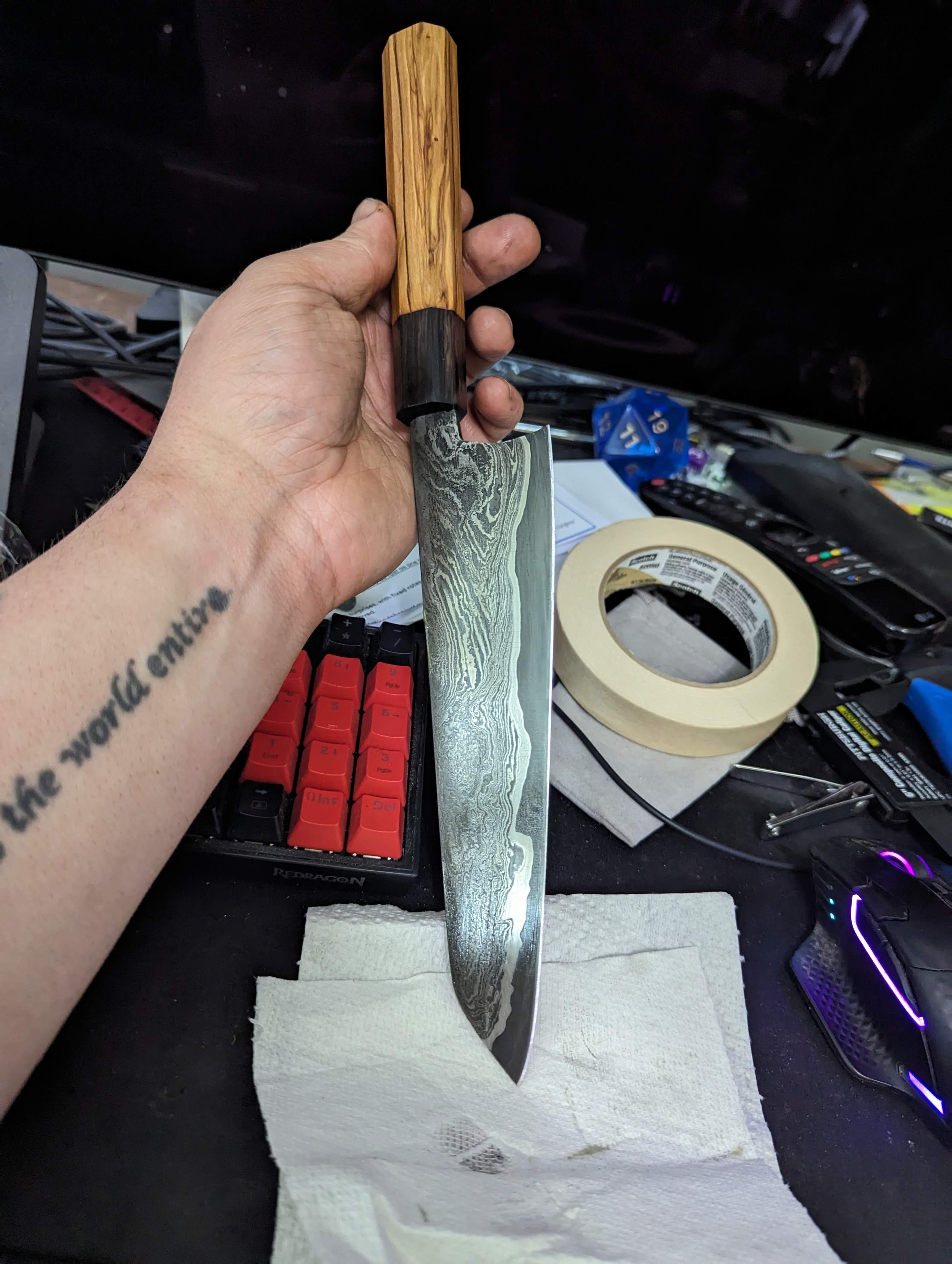